Um dos componentes mais importantes para a transformação digital da cadeia produtiva de spools para a indústria de óleo e gás (O&G) é a criação de simulações digitais de componentes e operações. Elas ajudam a entender melhor os processos e suas variáveis, reduzindo erros e aumentando a eficiência.
Neste post, veja os desafios da produção de spools de tubulação e entenda como um ambiente digital de simulação de processos de fabricação pode contribuir. Acompanhe!
Spool de tubulação: desafios da fabricação
A indústria de óleo e gás trabalha com estruturas altamente complexas. Isso faz com que a produção de componentes para atender às demandas do setor sejam igualmente desafiadoras. E é o que acontece com a fabricação de spools de tubulação.
Os spools são fabricados em instalações dedicadas conhecidas como pipe shops, seguindo uma sequência de operações bem definidas.
Embora boa parte dos processos seja finalizada já nos pipe shops, ainda há a necessidade de trabalho de campo, como o acoplamento a outros componentes — e em locais com alto grau de dificuldade de execução.
Por tudo isso, é preciso que a fabricação dos spools de tubulação aconteça de forma muito bem alinhada com o projeto a que eles se destinam. Caso contrário, a necessidade de retrabalhos pode gerar atrasos na obra, aumentar os custos e comprometer o retorno do investimento.
Sendo assim, cabe às empresas do setor buscar formas de reduzir a incidência de erros durante as etapas de fabricação dos spools de tubulação. E isso passa pela adoção de tecnologias e preceitos da indústria 4.0 aos pipe shops e aos processos de engenharia e produção dos componentes.
Ambiente Digital de Simulação de Processos de Fabricação de Spools
Dentre as inovações que a transformação digital proporciona ao processo de fabricação dos spools de tubulação está a implementação de ambientes digitais para a simulação de processos. Essa solução permite a análise e identificação de pontos críticos nos mais variados sistemas do chão de fábrica.
Conhecida como gêmeos digitais (digital twins), esta aplicação possibilita a construção de modelos digitais capazes de reproduzir processos físicos reais em um ambiente digital. Na figura a seguir é apresentada modelo digital representativo de um pipe shop
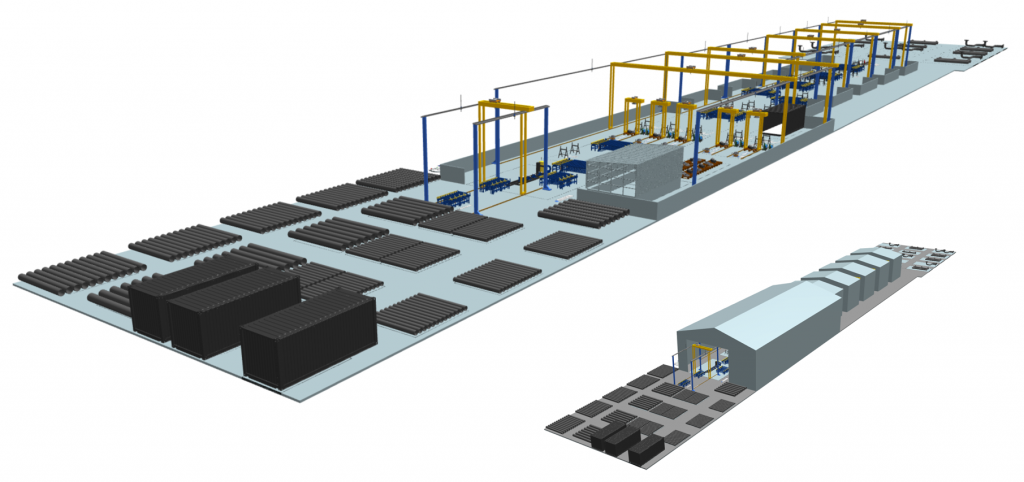
Isso garante a visualização detalhada das operações e suas variáveis no ambiente fabril, tornando essa tecnologia um fator fundamental para uma melhor tomada de decisão.
Os cenários simulados podem:
- Representar processos produtivos
- Validar soluções para layout
- Avaliar movimentações logísticas
- Identificar e promover uma melhor distribuição de recursos ao longo do processo produtivo
- Ajudar na busca por melhorias que tornem as atividades e operações mais eficientes.
Quando integrados a uma plataforma PLM (Product Lifecycle Management), os ambientes digitais para gerenciamento de ciclo de vida do produto são essenciais para a integração dos dados mais relevantes do componente e do processo de fabricação, além de serem um repositório único e centralizado de todas as informações geradas ao longo da sua criação. Como referência, na figura abaixo são apresentadas algumas das vantagens potenciais derivadas da utilização das plataformas PLM para a condução de projetos.
Nesses ambientes, é possível identificar e detalhar os diferentes aspectos envolvidos na fabricação dos spools de tubulação, como por exemplo:
- Requisitos de produto
- Variáveis de fabricação (dados de corte, solda)
- Detalhamento de processos
- Infraestrutura de fabricação
- Capacidades produtivas
- Especificações de matérias-primas
Uma vez que os dados estejam disponíveis na plataforma, pode-se simular um gêmeo digital do processo produtivo. As integrações criadas entre os diferentes grupos de informações e o detalhamento dos fluxos produtivos possibilitam, também, outros tipos de análises, como custos, simulações de cenários produtivos e previsões de prazo de fabricação.
Benefícios da simulação da fabricação de tubulações
Ao contar com um ferramenta capaz de transmitir as melhores respostas, os dados necessários para a elaboração dos gêmeos digitais se tornam chave para as etapas de construção dos spools de tubulação.
Com base nessas informações, a simulação consegue emular os processos físicos e representá-los fielmente. Assim, torna-se possível realizar estudos utilizando os conhecimento dos processos para propor melhorias, trazendo benefícios como:
- Mais assertividade no atendimento das necessidades dos processos;
- Maior previsibilidade para a alocação de recursos;
- Otimização e acompanhamento diário da produção;
- Possibilidade de acompanhamento das entregas e prazos junto aos fornecedores;
- Redução do investimento na ampliação das instalações;
- Visibilidade de todo o processo na cadeia de suprimentos.
Além disso, o ambiente produtivo digital e integrado traz um componente vital de rastreabilidade, assegurando uma maior segurança para os processos.
E isso vale tanto para um cenário onde se busca somente o armazenamento das informações, quanto para situações em que sejam necessários dados críticos para a correção de erros de fabricação, para melhorias operacionais ou para adequação do fluxo produtivo.
Para mais conteúdos e informações sobre transformação digital, indústria 4.0 e processos inovadores, continue acompanhando o blog da Certi.