Apesar de o Brasil ser um país populoso, rico em recursos naturais e com parques industriais desenvolvidos e maduros, a indústria 4.0 no país ainda é uma realidade distante. Tecnologias como Inteligência Artificial, Robótica e Internet das Coisas (IoT) ainda não fazem parte da realidade de uma grande parcela do setor industrial.
Abatido por constantes crises, o Brasil tem o desafio de se alinhar às tendências de digitalização da indústria que vêm sendo adotadas ao redor do mundo, a fim de se tornar mais competitivo no cenário global.
Neste post, vamos abordar o conceito e o cenário da indústria 4.0 no Brasil, seus benefícios, por que ainda estamos tão atrás de outros países nesse quesito e o que fazer para impulsionar o uso de novas tecnologias na indústria nacional. Acompanhe.
O conceito da Indústria 4.0 e os pilares para a transformação
Também chamada de Quarta Revolução Industrial, o conceito de indústria 4.0 trata principalmente da automação de processos e da digitalização da informação industrial, que combina as tecnologias mais atuais para conferir competitividade aos negócios e reduzir custos.
Seu objetivo é promover uma descentralização dos processos por meio do uso de diferentes tecnologias interconectadas que permitam controlar toda a cadeia produtiva e de logística. Trata-se, em outras palavras, de realizar a fusão entre os processos físicos, digitais e biológicos da indústria.
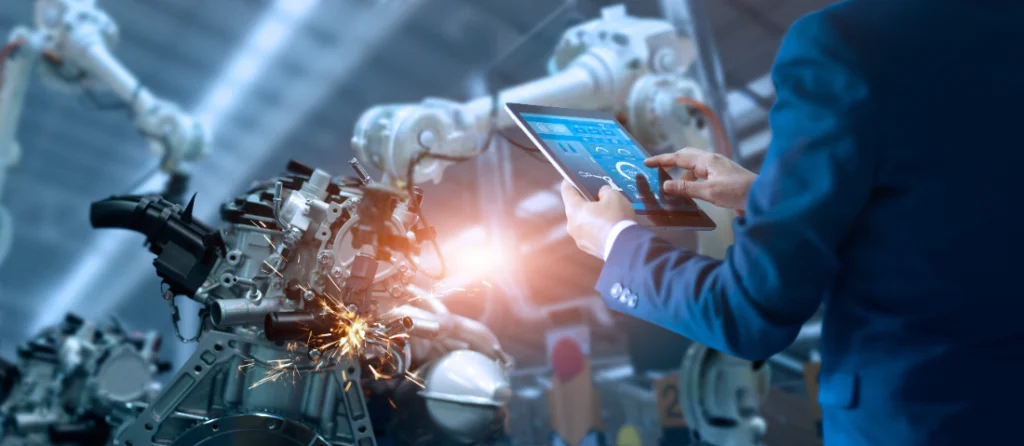
Os principais pilares tecnológicos para essa transformação são:
- Big Data: análise de grandes volumes de dados;
- Computação em nuvem: é o compartilhamento e armazenamento de dados totalmente online, melhorando o tempo de resposta e garantindo mais segurança aos processos.
- Manufatura aditiva: impressão 3D, por exemplo;
- Inteligência Artificial (IA): automação e aprendizado de máquinas;
- Internet das Coisas (IoT): mais especificamente, Internet das Coisas Industrial (IIoT), promovendo a interconexão entre máquinas e dispositivos conectados à rede;
- Sistemas Ciber Físicos: criação de cópias e de gêmeos digitais de equipamentos e processos;
- Biologia Sintética: combinação de química, biologia, ciência da computação e engenharia.
Impactos e benefícios da Indústria 4.0
A indústria 4.0 trará – e já traz – um impacto profundo em toda cadeia produtiva global, embarcando uma série de tecnologias que permitirão o uso mais eficientes de recursos (físicos, financeiros, informacionais e tempo) e, como consequência, tornará produtos e serviços mais competitivos.
A quarta revolução industrial também traz ganhos para a produtividade das indústrias, promovendo a redução de custos e um maior controle sobre o processo produtivo.
E isso representa uma verdadeira revolução nas plantas fabris, uma vez que todas essas inovações se unem para proporcionar modelos de gestão mais eficientes e nortear a tomada de decisões com base em dados coletados e analisados em tempo real. Essas informações se revertem em um aumento da capacidade preditiva da indústria, seja no que se refere à manutenção ou a demandas e a novas oportunidades de mercado.
Com a eficiência de sistemas autônomos e inteligentes, é possível reduzir ao máximo os desperdícios e a ocorrência de falhas na produção, alinhando os processos produtivos à demanda de um mercado cada vez mais exigente.
Para se ter uma ideia, a Agência Brasileira de Desenvolvimento Industrial (ABDI) estima que, ao migrar a indústria brasileira para o conceito 4.0, haverá uma redução anual de custos industriais de, no mínimo, R$ 73 bilhões. Isso envolve ganhos de eficiência e redução de custos de manutenção e consumo de energia.
Cenário da indústria no Brasil
A crise econômica da qual o Brasil ainda não se recuperou plenamente e os impactos da pandemia do novo coronavírus afetam diretamente a indústria, que hoje representa cerca de 11% do PIB do País, de acordo com dados da ABDI. A má notícia é que este índice vem caindo. Na década de 80, por exemplo, a indústria representava mais do que 20% do PIB brasileiro.
Além disso, o Brasil vem caindo no Índice Global de Inovação de 2020, que avalia a performance das nações no que se refere ao crescimento da produtividade, investimentos em P&D, educação, entre outros.
No ranking liderado por Suíça, Suécia, e EUA, o Brasil aparece apenas na 62ª posição. Já no Índice Global de Competitividade da Manufatura, feito pela consultoria Deloitte, o Brasil caiu da 5ª posição em 2010 para a 29ª em 2016, em um ranking que avalia 40 países.
Embora a indústria 4.0 no Brasil possua uma tendência a ser bem sucedida, de acordo com o último relatório Readiness for the Future of Production Report, elaborado pelo Fórum Econômico Mundial (WEF), em 2018, ocupamos apenas a 41ª posição do ranking. Segundo o documento, a estrutura de produção do País possui baixa complexidade e, juntamente com Argentina e África do Sul, conta com os menores índices de preparo entre as nações do G20.
Mas nem tudo são más notícias. Segundo o relatório, o Brasil segue sendo um grande atrativo para investimentos estrangeiros e pode se beneficiar de suas relações com outros países para facilitar a transferência de conhecimento e tecnologia.
De fato, já contamos, no Brasil, com indústrias que possuem um alto nível de inovação e maturidade digital, como as do setores farmacêutico, automobilístico e de alimentos e bebidas.
Outros, como é o caso do agronegócio, possuem alta penetração das inovações tecnológicas em seus processos, mas ainda carecem, de forma geral, em conectividade, recurso fundamental para trazer mais eficiência ao setor.
Desafios para a indústria 4.0 no Brasil
A transição para a indústria 4.0 é gradual e não ocorre de uma hora para outra. Muitas indústrias já utilizam alguns dos conceitos de manufatura digital, mas ainda não migraram totalmente. Isso acontece por alguns motivos, como:
Fornecedores desatualizados
Toda a cadeia produtiva precisa se adaptar aos novos tempos e isso inclui os fornecedores da indústria (supply chain). No entanto, em alguns setores, essa mudança tecnológica está ocorrendo de forma mais ágil e, em outros, de forma um pouco mais lenta. Equilibrar todos os setores é um grande desafio.
Investimentos altos
Toda mudança exige um nível de investimento e, com a conjuntura econômica atual, muitas empresas ainda têm receio de investir, apesar dos inúmeros benefícios comprovados que são trazidos pela indústria 4.0. As que investem o fazem com cautela.
Infraestrutura defasada
Para a implementação da manufatura digital, é necessário uma infraestrutura bastante potente, que inclui redes móveis e internet de alta velocidade (em especial, fibra óptica), devido ao grande fluxo de informações durante os processos industriais.
Mudança de cultura
Um grande desafio é a transformação cultural para a indústria 4.0 no Brasil. Isso porque a cultura de uma organização é moldada por meio de todo um processo e geralmente está bem enraizada nos colaboradores. Essa grande mudança de paradigma, proposta pela manufatura digital, pode trazer bastante resistência e precisa ser realizada gradualmente.
Como impulsionar a indústria 4.0 no Brasil
Em meio a esse cenário de desafios, a boa notícia é que existem iniciativas para estimular o desenvolvimento da indústria 4.0 no País. O Ministério da Economia instituiu o Grupo de Trabalho para a Indústria 4.0 no Brasil (GTI 4.0), ainda em 2017, elaborando uma agenda para o tema com a reunião de mais de 50 instituições representativas, que envolve governo, empresas, sociedade civil organizada, startups, entre outros players.
As medidas que estão em andamento visam a fomentar a indústria 4.0 no Brasil e incluem, por exemplo, difusão de conhecimento, apoio às indústrias e facilidade de financiamento junto a bancos públicos.
Dentre os temas prioritários debatidos pelo grupo estão o aumento da competitividade, as mudanças nas estruturas das cadeias produtivas, as fábricas do futuro, o uso de tecnologias digitais, entre outros.
Como a própria ABDI ressalta, são necessárias estratégias empresariais e políticas públicas que promovam um amplo debate no setor produtivo para auxiliar as empresas brasileiras em sua trajetória rumo à digitalização da cadeia produtiva e da manufatura nacional.
Para isso, a agência pauta quatro premissas para o desenvolvimento da indústria 4.0 no Brasil. São elas:
- Fomentar iniciativas que facilitem e habilitem o investimento privado, haja vista a nova realidade fiscal do País;
- Propor agenda centrada no industrial/empresário, conectando instrumentos de apoio existentes, permitindo uma maior racionalização e uso efetivo, facilitando o acesso dos demandantes, levando o maior volume possível de recursos para a “ponta”;
- Testar, avaliar, debater e construir consensos por meio da validação de projetos-piloto, medidas experimentais, operando com neutralidade tecnológica;
- Equilibrar medidas de apoio para pequenas e médias empresas com grandes companhias.
LabFaber: um laboratório que fomenta a indústria 4.0
Fazer investimentos em equipamentos e tecnologia para adequar a planta industrial ao modelo 4.0 exige pesquisa e desenvolvimento. Nesse sentido, uma forma de evitar riscos e investir de forma certeira é testar em ambiente controlado e especificamente pensado para os projetos industriais.
Foi pensando nessas necessidades que a CERTI criou o LabFaber, uma plataforma para desenvolvimento, experimentação, disseminação e capacitação voltada para transformação digital da indústria e com foco no desenvolvimento e na competitividade das empresas.
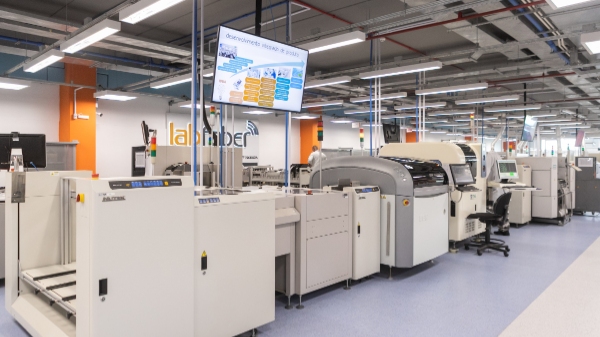
O LabFaber disponibiliza à indústria todas as tecnologias essenciais de indústria 4.0. Ele permite emular com detalhes uma instalação fabril real, monitorando-a para reproduzir as condições de operação.
Desde a concepção da ideia do produto ou do processo de manufatura até a prototipagem e colocação no mercado, utiliza uma infraestrutura com processos totalmente monitorados, sensorizados e instrumentados para ser um grande laboratório de indústria 4.0.
Dentre as principais vantagens competitivas que o LabFaber pode fornecer à indústria, destacam-se:
- Aumento da produtividade;
- Automatização de processos;
- Inovação com inteligência;
- Otimização de recursos;
- Planejamento a longo prazo;
- Redução de interrupções.
O LABfaber da CERTI configura-se como um laboratório-fábrica de referência no desenvolvimento, domínio, prática e difusão de tecnologias digitais na manufatura competitiva de produtos tecnologicamente avançados, e à capacitação e disseminação de soluções em Indústria 4.0. Ele sucede o exitoso LABelectron, ampliando agora seu escopo de “Placas Eletrônicas” para “Produtos Mecatrônicos” com elevada densidade tecnológica, por meio de um projeto mobilizador apoiado com recursos da Lei de Informática no contexto do Programa Prioritário HardwareBR. Os investimentos previstos à consolidação do LABfaber no período 2019-2022 são da ordem de 56 MR$, a serem captados junto às empresas via PPI.
Conclusão
A indústria 4.0 está em franca expansão em todo o mundo e é, certamente, o futuro das indústrias em nível global, acompanhando o processo de inovação trazido pelas mais recentes tecnologias, como Internet das Coisas Industrial, Big Data e outras.
Embora ainda esteja em estágio inicial, a indústria 4.0 no Brasil conta com importantes programas de incentivo para sua viabilização. Sua adoção deve acontecer de forma gradual, pelo menos enquanto o País se recuperar dos impactos da crise e da pandemia.
No entanto, mesmo com esses percalços, é fundamental o investimento e o fomento à digitalização industrial, visto que é preciso alinhar-se ao mundo para que a indústria nacional cresça e se desenvolva. As empresas podem se tornar parceiras da CERTI para desenvolver soluções customizadas e inteligentes para sua indústria. Quer saber como? Então acesse o e-book LabFaber: Plataforma de desenvolvimento, domínio, prática e difusão das tecnologias centrais da indústria 4.0 e saiba como o laboratório-fábrica da CERTI pode auxiliar a sua empresa!